At setups which are on one side and at room temperature and on the other end cooled down by a cry head to almost zero kelvin (-273°C) a huge thermal gradient is given. Therefore, thermal contraction of the connecting part made of steel or any other material might lead high shear stresses at the cold head, where it is mounted to be cooled down. However, to efficiently could down or even to reach cryogenic temperatures a several component hinge is not usable.
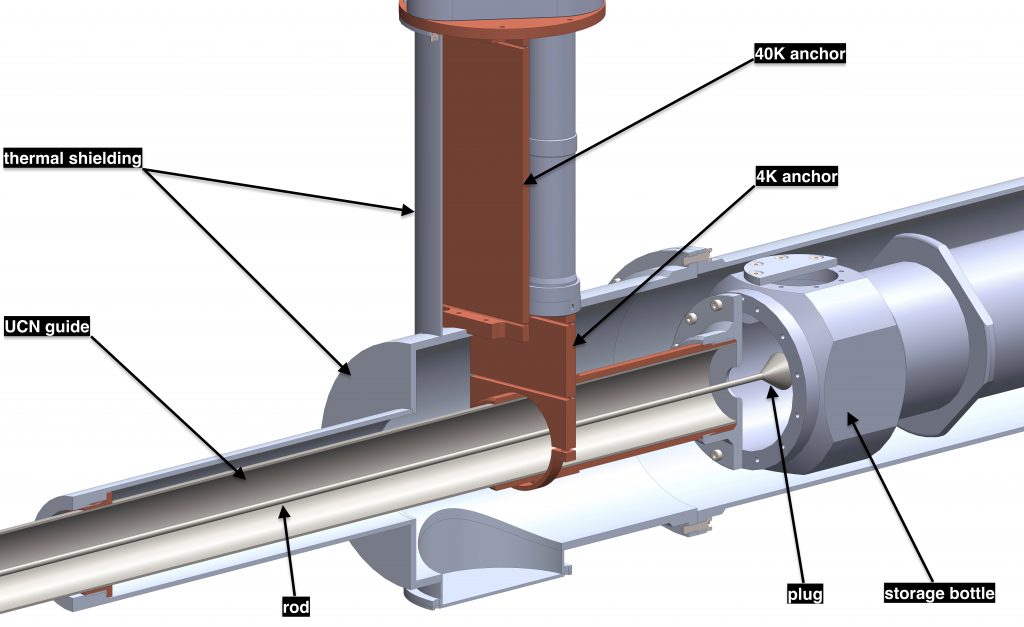
As solution elastical hinges are usable. The calculation to chose the dimensions of those is done according to the equations provided by Koster, M.P. in Constructieprincipes voor het nauwkeurig bewegen en positioneren [Twente University Press and others, 2008.], together with the rule of thumb for the elastic hinge parameter β defining the functionality of the hinge with an elastic range between 0.01 < β < 0.5, where the lower bound presents the minimum machineability and the upper the hinge functionality.
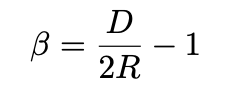
Here R is the radius and D the minimum distance between the centers of the corresponding circles. To find an optimum between the given boundaries, the minimum heat transfer area is identified by solving the one dimensional heat transfer equation while respecting the variable heat capacity of copper towards cryogenic temperatures and simulating the maximum applicable lateral forces within CAD simulation software.
Further information on this subject can be found in my master thesis. We also would be glad to help you designing, manufacturing or conducting stress simulations of your hinge. CONTACT US
